Aki Machida
LPD(Laser Phospher Display)の構造と世代ごとの問題点、課題について解説するとともに、プロセスの中国移管がどれほど大変だったかについて実体験談を紹介します。そして転職、解雇、解雇、独立。
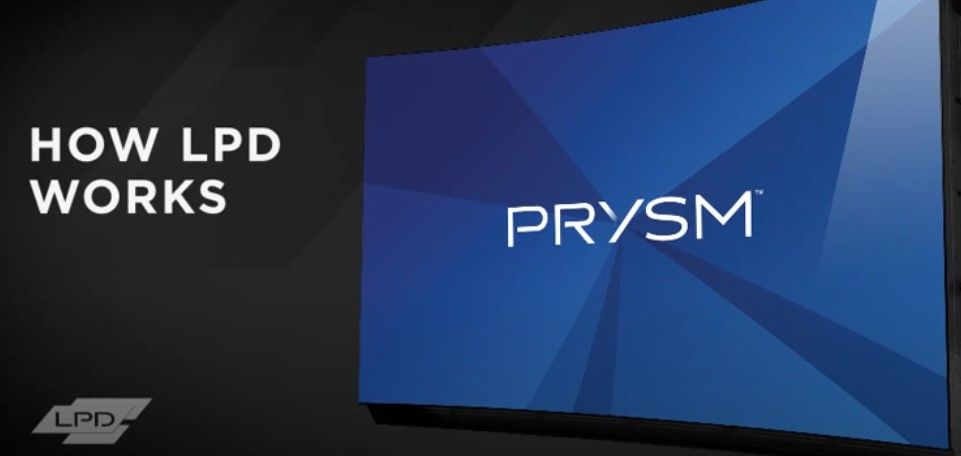
台湾・中国への移管の前に、忘れていはいけない数々の不具合対策を列記しておきます。まずはPRYSM社の初期製品であるLaserPhosphorDisplay、LPDについて仕組みを解説したYouTubeがあります。高出力の紫レーザを束ねて機械的にラスタースキャンして、蛍光体を印刷した表面を励起させ、映像を実現します。ベゼルが無いので、上下左右に並べることで200インチという巨大なディスプレーを完成させます。重さは1トン近くになります。しかし、消費電力は1KWと低く、部屋の冷房も少なくて済むという優れ物です。
YouTubeはこちら How LPD Works
事業場所の説明をしておきます。シリコンバレーの本社は電気やディスプレーの評価が主な開発業務で、光学系やメカはボストンのMIT卒の軍団が担ってました。ソフトはインド。能動部品などは日本のベンダー10社ほどで、ディスプレー表面部分製造はタイ・バンコック、電気系の製造委託は台湾、東莞、そして上海の北の連雲港にちらばっていました。
ブルーレーザ#1(バーンイン)。当時405nmのハイパワーレーザは3社しかありませんでした。トップメーカに続く家電メーカの2社。特許侵害していたのかもしれないものの、特注品取引のため、そこは定かではありません。我が社のCEOもCTOも高級ドイツ車に乗っていたとは言え、お金にはうるさく、結局一番安い広島のメーカからの調達でした。種を明かすと、値下げの為に、レーザで最も重要なバーンインという初期不良を取り除く工程を全数しないという取り決めにしたのです。当然、そんな事は許されるわけもなく、多数の不良在庫を抱える事となり、ジャンク屋送りとなりました。日本語で言う、安物買いの銭失いです。
ブルーレーザ#2(トップメーカの怒り)。お客様とパートナーからの信頼を得るために、四国のトップメーカから調達しようとしたのに、試作から量産に移行する際、先の低品質のメーカに切り替えたため、プライドを傷つけてしまい、いざという時に売ってくれません。激しい値下げ交渉の末、新米の購買部長が事もあろうに開発中で量産の目処が立ったばかりの第3のメーカの存在を明らかにしてしまい、トップメーカの担当営業部長は呆れて怒って帰ってしまいました。結局、私が駆り出されて、四国まで行って頭を下げて、売ってくれることになりました。YHPの営業時代から、購買は超上から目線でいい仕事だなと思ってました。いざ、スタートアップの調達を始めると全く逆です。信用されてませんから、交渉は全て前金が条件で、歩留まりも出たとこ勝負です。結局この第3メーカと取引することになり、私は品質確認で工場監査で富山まで行き、私がHP時代に築いたトップメーカとの友好関係は心無い同僚や上司にブチ壊されてしまいました。
ブルーレーザ#3(コリメータの中国工場)。レーザはコリメータという光学ユニットに押し込まれます。レンズの位置を調整する機構の付いたスイス時計のような高価なものです。数が増えたので、日本の超有名部品メーカにライン設立投資をして、東北の古河工場から東莞工場にライン移設しました。最初の監査の時は良かったものの、生産を始めると色々不具合が出てきます。静電気破壊やゴミが目立つようになったので、再度工場に行くとエアーシャワーがありません。天井のビニールもなく、クリーンルームがリセットされていました。当然蚊がラインに入って来るので、蚊取り電撃ランプが入り口にあってバチバチ音を立てて蚊を退治していました。そして落ちた蚊を工員が踏んで歩きまわります。開いた口が塞がらないとはこのことです。東莞工場長は「エアーシャワーの効果が無い」という理由で東北工場長に許可を得ない独自判断でした。毎週月曜の朝はホコリが沈下してますからクラス1000を満たしているということでした。でも操業一時間後には100万近い数値となります。即刻直して改めるよう、要請しました。
パネル品質#1(アイセーフティ)。単なるRGBの蛍光体を印刷しただけのシートでは淡黄色の為、コントラストは最悪ですから、LCD同様、カラーフィルターを使おうという事になりました。ただし、高出力のレーザを扱う以上、EyeSafetyのUL規定に合格しなくてはいけません。つまり、弾丸が打ち込まれた時、スキャンするレーザの光が開いた穴から出てきてはいけないという規制です。そこで、酸化クロム製のブラックマスクのパターンを時定数を元にグループ毎に繋ぐことを提案しました。これで音速で飛んでくる弾丸がパネルを通過する前にレーザをシャットダウンできる回路を作り上げ、特許登録しました。これは土曜日のブレインストームだったので、参加者全員がインベンターになっていますけれど、はじめの一歩は私です。
https://image-ppubs.uspto.gov/dirsearch-public/print/downloadPdf/20100244705
パネル品質#2(ベンダーの倒産)。皆さんが目にするLCDはRGBのフィルターが黒いブラックマスクによって区切られています。この黒い細い線はクロームメッキを使う方法とホトレジストを使うリソグラフィー法があります。クロムメッキは環境にも人体にも影響が無いとは言えないので、日本にはサプライヤが2社しかありませんでした。前述のアイセーフティの為、現在主流のレジストタイプは使えません。したがって、そのうちの東北の1社に製造装置の費用負担もして調達をしていました。ところが資金繰りが悪化して倒産してしまいました。スタートアップによる製造依頼は、材料を前金で買って、経理上支給という形を取ります。つまり、倒産した会社の工場内には、こちらの所有である材料が大量に残されたまま、差し押さえとなり、電気も切られちゃいますから、低温保存も出来ず、最悪の場合全数廃棄になってしまいます。早朝、倒産情報が電話で入り、CEOと対策を確認して夜の便で日本に飛んで、PRYSMに投資していただいているVCパートナーの方と雪の中を時々右側通行しながら工場に行き、管財人の方と面会して、材料と当社所有の製造装置に関しては幸いにも搬出許可を頂けました。マイナス20度で保管しなければいけない材料は、仙台の野菜市場の冷凍庫を借りて、保管場所としました。この製造協力会社は3つの子会社から成っていまして、製造装置を移す度に連鎖倒産を繰り返し、結局最初の会社が更生して製造を継続してくれました。この件は落ち着くまで、毎月のようにいわき、仙台、八戸、六ケ所村と飛び回っていました。
パネル品質#3(スクリーン印刷)。蛍光体の印刷は粘度の高い溶剤を使うので、スクリ-ン印刷をします。会社設立当時の製造パートナーが印刷の大手企業だったこともあり、その会社がプラズマディスプレイ用に使っていた新潟のスクリーン印刷装置を使うことにしました。業界の巨匠のような方を紹介して頂き、ステーキディナーで接待して、レオロジーだなんだかんだとワインが空になったところで、結局「練習するしか無いんだよ」という極意を頂きました。そこで、他力本願を止め、印刷機を買って、ノウハウを自分たちで築きあげようということになりました。価格と納期で散々交渉した挙げ句、ボストンまで2.5トンの装置を空輸したのです。ボストンの開発グループはデジタルエキップメント(DEC)という会社が発祥したメイナードのレンガ造りのコワーキングスペースにありました。MIT卒業メンバーのエリート集団が入念に搬入手順書を用意したにもかかわらず、搬入用のエレベータには乗るものの、別館に移動する通路がアーチ状のレンガの門の向う側にあるために、搬入当日に中止となってしまいました。あるあるアメリカです。レンガ造りの建物は州の保存指定になっているので、おいそれと壊したり傷つけたりできません。急遽そのゲートのサイズを確認し、装置のモニターやパトライトを外して90度横向きにさせれば通過できることを提案しました。当然、「そんな事できるわけねーだろ」と言われましたけれど、エジプトのピラミッドの石の移動は丸い木枠で囲むことで転がせた逸話を引っ張り出し、現地の搬入業者が了承。無事搬入できたというわけです。雑学がMITより役に立ちました。笑。
出所:http://utzsugi-rei.com/utzugi/images/Pyramid/pyramid_slope3.jpg
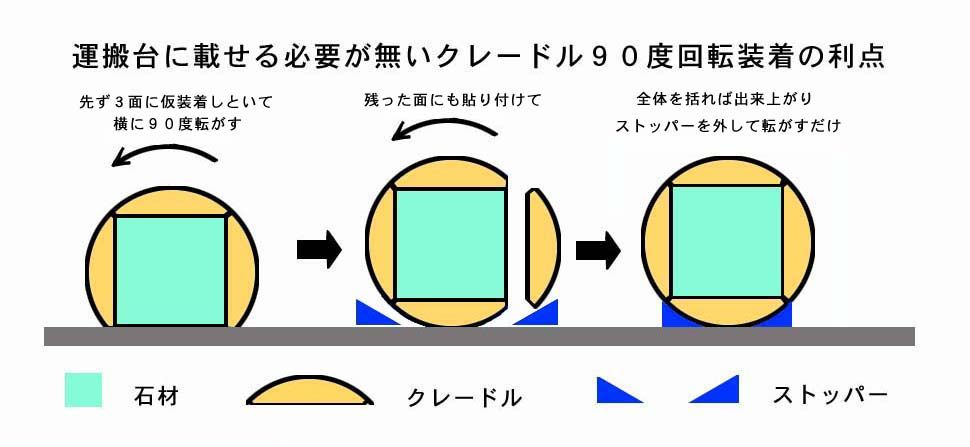
パネル品質#4(複屈折)。レーザからの光線はポリゴンやガルボを使います。ただし、仰角が狭いので、25インチのパネルをオーバースキャンするには内部に鏡を2枚使います。FoldingOpticsですね。ところがレーザは偏向光のため、ところどころに使われているPETのような複屈折率材料の影響を少なからず受けます。ランダムな場所で405nmが通過しにくくなり、明暗が出てしまうのです。複屈折率測定器メーカやらPET材料メーカにペインポイントを伝えてソリューションを探しました。結果、沢山買って良いロットを選んで、正しい方向に整列させて切り出すしか無いということがわかりました。そこで、対策を講じたものの、とんでもなく複雑で手間がかかるので、結局レーザの出力を上げて、マッピングという方法でピクセル単位で輝度調整をすることで、難局を乗り切りました。
パネル品質#5(ゴースト)。前述のようにフォールディング・オプティックス構造のため、ゴーストの問題が出てきます。検査は簡単で、暗室で真っ黒な画面にゴルフボールくらいの白い球の映像をゆっくり上から下にジグザグに表示すると、いろいろな位置にゴーストが出てきます。レーザダイオードから出た光が観察者の目に届くまで、内部界面が30近くあるので、対策も用意ではありません。対策を全く施していない部品と入れ替えれば潰せるものの、一つ一つ製品を組み直してゆくのですから、気が遠くなるような時間がかかりました。私の担当部品では、レーザダイオードの缶の窓ガラスの傾きとか、ガルバノメータのシリコンミラー、ポリゴンミラーの反射率、表面反射鏡、5ミリ厚のガラスの無反射コート、シートフレネルの基材選別、フレネル表面の無反射コート、カラーフィルターのピラー材料の黒色化、などです。これだけ担当出来ればやり甲斐十分でした。大学の卒業研究がスパッタリングだったので、やっと当時の経験が役に立ちました。尚、どうやってカマボコ型の蛍光体を印刷するかとか、波長選択シート、サーボパターンの印刷方法など、かなりの内容がトレードシークレットとなっています。特許申請はCTOの判断です。公にされて困るノウハウは特許という形で公開情報にはしないということを学びました。
ガルバノメータ品質(シリコンミラー)。20個の4Wという高出力レーザを束ねて上下に光を振るガルバノメータ(ガルボ)には99%以上の超々高反射率のシリコンミラーを使います。でないと、ミラーの支持体が高温で溶けてしまいます。しかも超々平坦でないといけません。たとえで言うと絶対にゴルフボールが曲がらないグリーンを作るような難しさです。ですから、蒸着膜を付ける前に磨いたシリコンウエハーを干渉計で検査した上で、真空蒸着で無反射膜をつけてゆきます。干渉計は高価なので、近くの工業試験場にお願いしました。こちらの所望のレンズを持っていなかったので、購入して寄付しました。どれくらいの膜をつけるかというと、50層以上です。しかも片面にいきなり50層つけるわけにはいきません。イカのステーキのように簡単にせり上がってしまいます。ですから少しづつストレスがかからないように表裏を慎重に蒸着します。装置を真空にするには1時間以上かかりますから仕上がるまで、気の遠くなるような日数がかかります。そしてこれを1センチ角に切ります。そうすると切った途端に均衡していたストレスが破綻して、ケシの種のサヤというか、イカ焼きのように反ってしまうのです。さらに電磁コイルの支持体に接着すると強力な接着剤が固化する際に1mmという厚さのシリコンをミクロン単位とは言え、逆方向の海老反りにしてしまうのです。もっと悪いことに接着剤の塗布とミラーの置き方によって、ミラーの下に気泡ができると、共振周波数が下がり、音が出たり、ディスプレーの画像フレームレートに影響が出ます。超音波による非破壊検査メーカを探して、その装置が日本のどこの工業試験場にあるかを探し当て、品質確認が製造現場近くで出来る手配をしました。ガルボに関しては出荷トレーの不備もあり、梱包個数の制限をかけたり、高級ワインを送るために開発されたハイテク・クッション付きの梱包なども用意しました。
空中放電?
ガルボの駆動はインターレースのためです。はじめに20個のレーザが1万RPM以上でで回転する8面すべて角度の違うポリゴンミラーで160ラインの奇数行を走査し、次の回転で、偶数行を走査しますので、8番目の面から次の1番目の面に変わる間に、超高速でほんの少しだけの角度でオーバーシュートやリンギング無く、カチッカチッと動いてくれないといけません。そのため1Aほどの出力を持つDAコンバータを使います。最終的には320行ではなく、480行を操作する3ステート駆動をしました。人間の網膜自体は恐ろしいほどの追従性があり、大画面になると60FPSの画面ではチラついて見ていられませんので、240FPSくらいまでリフレッシュレートを上げる必要があります。ですので、最終的にはポリゴンモータの回転数も数万回転に上がりました。ところが、このDAコンバータは静電気に弱いので、製造委託先でよく壊れたのです。そこで、石川の工場まで監査に行ったところ、静電ストラップをしていなかったのです。オペレータさんは不思議な青い布を手首に巻いているだけでした。いわく、空中放電ストラップという代物で、オーディオ部品製造はこれで十分だったとか。静電メータと表面抵抗計を持っていったので、現場の確認です。驚くことに、静電マットもなく、床はリノリュームで歩けば指先に1万ボルトが出てくる始末。思わず腰が抜けそうになりましたが、こっちは弱小スタートアップ。冷静にデータを見せて対処し、キーエンスに電話を入れてイオナイザを必要数調達し、それ以外も対策を取ってもらいました。夕食はブランドの松葉ガニをご馳走になり、気を取り直しました。
ポリゴンミラー品質(チルトミラーとエアベアリングモータ)。レーザを機械的に上下左右にCRT(カソードレイチューブ、死語ですね)のようにラスタースキャンしますから、前述のように8面の角度が異なるチルトミラーを使います。研磨では作れないので、5軸のNCマシンを使います。当然安くはありません。PRYSMのディスプレーは屋内用のサイネージや貧素なプロジェクターを置き換える用途として(手前味噌ながら)最適です(今でもそう思います)。そこに夢を賭けていただいたM商事さんやT電機さんとのパートナーシップがあったお陰で、最大手のポリゴンミラーメーカが投資をしてくれました。
このメーカはポリゴンミラー用の高純度のアルミニウムを手掛ける大会社です。干渉計もお持ちで出来上がり品は十分な平坦度がありました。ところがチルトしているせいで、バランスがとても悪いのです。モータメーカで組み立ててもらうといきなり製品には載せられないことがわかりました。
ミラーだけでバランスを取ってから、取り付けるため、少量生産ラインはクリーンルームを使わせてもらえません。このモーターはエアベアリングと言って、回転し始めると空気の流入を使って、僅かな間隙を作り、空中に浮いた状態で高速回転してくれます。ちょっとのゴミが入り込むだけで、妙な音が出たりするのです。イオナイザーを使って、クリーンブースを作り、ゴミを拭き取る綿棒の種類を変えてもらったりしました。輸送中にモータの芯が筒にぶつかると芯が傷付き、場合によっては欠片がこの間隙に入り込むとおじゃんになります。輸送も量が多いとパレットになります。ただし少量の時は箱になります。データロガーを出荷してもらったら、なんと日本国内でも中国でも箱は放り投げられていることが分かりましたので、全ての出荷に対してパレット輸送で、箱を横向きにしないように手配しました。
生産ラインでも不良が出ていました。ラインに潜り込み、取り扱いを見ていると、組み上げたライトエンジンのテストが終わるやいなや、立てて使用するライトエンジンをすかさず横にしてしまうのです。回っている頭でっかちの独楽を横にしたら、軸が筒に擦れるのわかりますよね。呆れて、テストが終わってから、30秒待って、モータの回転が終わるのを確認してから向きを変えるように工程表を変えてもらいました。それまでの大量の不具合ミラーの再利用も試みたものの、中国の下請けでの支給部品に対する不良品管理はいい加減でしたし、モータメーカからも拒絶されたので、諦めました。
生産台数が増えてくると、USに到着した製品、特に光学エンジンのまま送ってもらった半製品がよく不良になります。騒音が大きく、画像も安定しません。調べるとモータの軸が傷付いていました。出荷方法を確認するとなんと横置きを積み上げてパレットに載せていました。梱包方法と積載方法を変えるように提案したものの、担当の中華系上司はプライドを傷つけられたと見えて、納得しません。しょうがないので、データロガーをパレットに載せて中国からサンフランシスコまで海上輸送をしてもらい、フォークリフトでトラックに載せたり、陸上輸送している最中に、不良を誘発するに十分な衝撃が加わっていることを証明しました。
YHP時代から、TQCのデミング賞を獲った頃から、三現主義と、データで話すという習慣が身に沁みていますから、それくらいの障害は、ちっとも応えなかったのです。
ディスプレーパネルのタイ協力工場への移管についてちょっとだけ触れます。
ボストンで蛍光体を小規模で印刷していたものの、数が増えてきたのでタイの工場と契約して生産ラインを構築することになりました。日本からスクリーン印刷機やアリゾナのフェニックスからガラスカッターなどを手配し、工場に搬入する際に現場立会いに行きました。日本からの機械は木枠に入っています。しかし全部釘留なので、開梱は大変でした。ところがフェニックスからの木枠はネジ止めなので、電気ドリルでさっさか外していました。こういうところは学びが多いです。
さて、暫く稼働していると雨期になりました。洪水です。タイの洪水は時間を掛けてゆっくり水浸しになり、どんどん水位が上がります。最終的に2mくらいの水位でした。機械や車は全部ビニール風船に入れて浮かばせたのには、びっくりしました。ただし、機械はバランスが悪く、着地したときに機械の角によりビニール風船が破れて総額数億円の機械は全部おじゃんになりました。私の上司が果敢にもインディアジョーンズと揶揄されながら現地を視察し、バイオハザードな生々しい写真が送られてきました。
保険が降りたので、今度は2階にラインを作り直しです。装置メーカには嬉しい2度目の注文でした。一度目には知らなかったB型肝炎の予防接種をちゃんと行なって、2度目の立ち会いに行きました。
中国移管の話に移りましょう。さてさて、PRYSMで7年過ぎた2015年頃から、スケーリングするということで、台湾・中国上海郊外のメーカに技術移転をし、製造委託をするということになりました。日本によく行ってましたから、ついでに台湾と中国も面倒見てくれということになり、開発購買役から生産技術の責務も負わされました。品質管理のおまけ付きです。
開発部隊の用意した製造マニュアルは、レシピ本みたいで、基本的に備わっているだろうというものは記述も仕様もなく、ある程度加工してあったものが突然出てきたり、途中の検査は抜けているし、出荷する梱包などは仕様もない状態でした。料理中に、既に水切りをした豆腐をここで加える、みたいなもので、最後はサイズや深さの記述がない皿に盛り合わせ、刻んだパセリを乗せます、みたいな、事細かな動作と治具を記した日本の作業標準(PCP)とは程遠いものです。
特に工員の教育レベルが低い中国では一挙手一投足すべて書き出しておかないと、「差不多(チャーブドゥ)」という魔法の言葉で正当化されてしまいます。ちょっとくらい違ったって、いいじゃないか、の意味です。これは本当に要注意です。https://www.youtube.com/watch?v=w9c4SuEPbIk&t=28s
ボストンの開発グループの動作をビデオに収めて、DVDを焼き、それを台湾と中国に送って中国語のPCPが作成されるものの、かなり端折られて、最後は差不多(チャーブドゥ)です。少しくらならいいいじゃないかというレベルではありません。Google翻訳で加筆に加筆をしました。中国語に関しては、USで通勤時間にPimslerという聞くだけの会話学習を続け、50レッスンを毎週1レッスン、車中で大声で復唱しながらこなしたおかげで、ちょっとだけなら中国人同士の会話でもわかるようになりました。
台湾の試作ラインで部品の入庫とモジュール製品の出庫がかなり少ないので、調べに行ったら、静電対策が取られておらず、高価なレーザダイオードがじゃんじゃん壊れていました。GaNの405nmのレーザは、DVD/CDピックアップの赤色レーザより、格段に静電気に弱いのです。なのにオペレータは静電ストラップを付けていない有様。静電気メータもGaNとなるとTrek社の物でないと正確に測れないのです。イオナイザをキーエンスの京都まで行って即買いし、費用の負担の話はトップに任せて、早急に対策しました。
中国のOEMラインにクリーンルームが出来たと言うので、10年ビザを入手して見に行ったら、静電テスト台で全員不合格になります。でも作業員は無視してガラスで覆われた部屋に入ってゆきます。静電テスト台が壊れているという言い訳でした。でも、何かおかしい。詳しく表面抵抗器を使って調べたら、クリーンルームウェアの布は導電繊維が効いていたものの、靴底の格子模様は偽物で、ゴムが完全に絶縁体になっていました。裸足になってテストしたら、ちゃんとOKになるじゃないですか。こんなことまでして、偽りを隠して、しかも現地の調達に罪悪感も責任感も無い状況で、目の前が暗くなりました。
コリメータレンズの固定も曲者でした。歩留まりを上げるために接着剤の量を多くして固着力を高め、接着力試験をパスさせれば、パスした部材もラインに戻せるので、損が少なくなるという猿知恵です。これを許可なくやられたおかげで、組み上がったコリメータを温度サイクル掛けると厚い接着剤が功罪となり膨張したり収縮したり、左右に動いてしまいますので焦点距離や位置がずれてしまいます。
もう一度温度サイクルを掛けると、またずれてしまいます。このミステリーを調べるには3現主義しかありません。朝からラインに入って空気のように振る舞い、溶け込んだ末に、遂に元凶を見つけました。結局、開発からの指示は2滴にも関わらず、中国のラインでは3滴使って接着強度試験の歩留まりや温度ドリフトを改善しようと、勝手にプロセスが変更さていました。結局、私が1滴プロセスを提案し、強度も温度サイクル安定性も最も優れたプロセスに変更できたのです。
他にも信じられないようなトラブルが次から次に起きます。トラブルが起きるたびに上海経由や香港・深圳経由で出張を繰り返しました。このPRYSM時代の10年でUnitedに100万マイル乗りまして、プレミアムゴールドのライフタイム会員になりました。
別の接着剤を滴下するプロセスは正しい位置ではなかったり、2液性の接着剤の硬化剤が効かずに24時間経ってもドロドロのままとか、滴下場所の指示間違いで固定化されていなかったり、デグリースされてない部品が入ってきたり、部品の検査していない仕様のばらつきで性能が左右されたり、散々でした。ステンレス部品を指定したのに価格の点で亜鉛メッキの鋼材に勝手に変えられていたりして、超音波洗浄後にサビが出るという体験もしました。
MIT卒のMEが作った工具が設計不良で、不良品を大量生産していたことも発覚しました。高出力レーザダイオードは放熱のために銅のプレートに圧入します。ところが、コリメータになった製品がディスプレーエンジンを組み上げる工場や、米国に来てから良く劣化するのです。劣化の原因はコンタミや駆動回路の問題も疑いました。不良解析をしているうちにレーザダイオードのカバーガラスの内側にキャッツアイマークが有るものが見つかりました。高出力のレーザ光がゴミを集めるトゥイーザ現象と呼ばれるものです。早速、四国のレーザダイオードメーカに不良解析をお願いしたところ、驚きの回答が出てきました。レーザダイオードの台座・フランジに斜めのマークが付いており、レーザダイオードが銅板に垂直に圧入されておらず、傾いて挿入されるため上部の缶が銅板の側面に触れ、封止ガラスが封止部分でクラックを発生し、窒素充填の缶内に温度サイクルの間に酸素が入り込んで、封止ガラスを汚して出力が下がるという内容でした。そこで、出力低下を起こしたコリメータをすべて分解して、銅板を切り開いたところ、すべてのレーザダイオードのフランジに斜めの銅の跡が付いていたのです。ひどいものはガラスが外れていました。これを治具の設計不良と報告したものですから、ボストンのMIT卒の軍団は黙っていません。納得させるのに相当な時間と労力がかかりました。きっと、とんでもない日本人だと陰口叩かれていたと思います。なぜ斜めに入るかとか、治具の改善をどうやったかは触れません。幸いエージングで取り切れることも電気のベテラン技師と確認しました。
プラスとマイナスを記したテストチャートの読み方がわからずにいたことを、中国側がずっと黙っていたのには開いた口が塞がらなかったです。全員中学卒業とのことでしたのに、愕然としました。この試験は缶入りのレーザダイオードの封止ガラスの傾きにより、ガラス内で反射と透過が起きるために強度分布のチャートの裾の部分に小さなリンギングが発生してしまうのです。ディスプレイの画面上ではクロストークとして隣のピクセルが光って白茶けてしまうのです。
レーザダイオードの供給メーカに治具を設置し、封止する前に測っておけば、歩留まりが上がって良いはずなのに、またもコスト重視のマネージャやCTOまでも反対され、結局、納入されたレーザダイオードの封止ガラスの表面傾斜を測って、5%程度の使用不可品をスクリーニングすることにしたのです。ただし、このテストチャートが低学歴の工員には仇となりました。
正の領域は右に行けば増えるので、ちゃんと読めるのです。しかし、負の領域は、例えばマイナス0.8はマイナス1.2と読むわけです。右に行けば増えるのでマイナス1の右側に傾き検査用のレーザの点が光るとマイナス1.2になるわけです。全部のレーザダイオードにシリアル番号を振ってましたから、マイナスの検査結果品はすべて再検査しました。テストチャートも左の合格ラインをゼロにして全部正の数字で読めるように変更し、入力データから、本来のゼロ点の数字を引いて、分布図作成とスクリーニングを実施しました。
実はこの問題の前にチャートそのもののスケールが間違っており、全数合格してしまうという珍事もありました。メーカであらかじめガラス面の角度を測ってもらったキャリブレーションサンプルとぴったり2倍の差があることで、チャートのチョンボを指摘しました。私の幾何の学力がMITを超えていた優越感は持てたものの、丸一日無駄にしました。中国工場とボストンの開発グループとは12時間の時差ですから、はっきり言って、眠る時間が相当削減されていました。
ラインは既に止まっているので、別工場で部材を待っている工員には、工場に来て何もせずにタダメシ食って帰るだけなのに、給料を払わないといけません。強烈なプレッシャーで、更衣室で休んでいるところに、トドメが来ます。
休憩から戻った工員がクリーンルームに入る前にガウンのポケットからナイトリルの使用済み手袋をさり気なく出して手にはめ、入室していきました。崖から突き落とされた気持ちでした。
中国人は鳥でも豚でも骨まみれの味付け料理を好んで食べますし、安いのでしょうから、工場の朝食やランチは大抵そういうおかずです。口の中の骨は手でつまみ出してテーブルの上に撒いていきます。手洗いもいい加減で、一度使って裏表になった手袋に手を通すわけです。もしかしたら、何日も使っているかもしれません。道理でコンタミネーションが無くならないわけです。パルスで4Wという超高出力レーザを使いますから、揮発成分があるとレーザの透過地点に気体が集められて透過率を下げたり、散乱要因となってしまいます。しかもこの問題は出荷試験ではわかりません。客先に出荷されて、ある程度使用期間が過ぎてから、市場不良として戻ってくるのです。
ま、手を打ちましたけれど、これらが原因で、旅程を延ばしたために帰りの乗継便がなくなってしまい、上海で交渉の末、自分のマイルを使ってシカゴ経由の飛行機の最後の1席を確保しました。
悪いことに、機内で右の頬に異変を感じます。頭痛もしてきました。なんと60歳になったのに忙しすぎて帯状疱疹のワクチンをしてなかったのです。家に戻って強烈な頭痛で寝てました。トイレに起きて洗面所の鏡に写った自分の顔は半分ケロイドで崩れていました。すぐに救急に行ったものの、抗生物質の投与が一日遅れ、治癒には相当な時間がかかりました。
いまでも免疫が下がると右頬が疼くので、免疫レベルのバロメータになっています。笑い事ではありません。当時はアイスパックを頬に当てて就寝し、痛み止めも長いこと服用しましたから、もしかしたら肝臓を痛めたかもしれません。
発病から6ヶ月でケロイド跡が消えたところで、転職を決意しました。
人生には色々な価値観があります。最も大切なのは、失うことの出来ない健康、妻、家族、親、腹心の友でしょうか。失っても死なない、仕事、金、ネットワークや趣味が次に来ます。自分としてはやれることは全部やりましたので、健康第一で、早期引退も視野に入れました。このことは価値観のブログとしてまとめてあります。
こんな自分でも受け入れてくれるところがないか、知人をあたっていたら、かつての上司、光学マウスを世界的な成功に導いた時の事業部長が社長をやっている量子ドットのNANOSYSがオファーをくれました。
価値観として大切な第2グループに、ネットワークがあります。年代や状況によって、価値観の重要性が入れ替わります。この時ばかりは健康とネットワークでした。
そして 61歳になって、PRYSMの第3世代が市場発表された2018年3月16日金曜日に退社しました。
(ちなみに新製品はここに紹介されています。https://www.prysmsystems.com/displays/lpd-6k-series/features/)
そしてその翌週月曜日にはNANOSYSに初出社し、個室をもらって次世代量子ドットのシニア・マーケティング・プリンシパルの生活が始まりました。
自分へのご褒美として、バッテリーが劣化した日産リーフやプレミアムガソリンを大食いする故障の絶えないベンツのSUVを下取りに出して、TESLA-3を入手しました。
会社は順調だったものの、トランプ1.0の対中政策に巻き込まれ、事業拡大案が凍結されることになったので、あえなく一年で、初めて失業保険をもらう身となりました。
2019年の夏は暫く日本での事業開拓をしていました。ここでもネットワークが活きて、富士フイルムの子会社に就職が決まりました。ここの社長はかつてのHP時代のお隣の事業部長で私のリーダー研修のメンターでもありました。
ショールームを起点としたビジネスデベロップメントをするオープンイノベーション活動の現地マネージャとして就任したものの、すぐにコロナが始まってしまい、誰も来ないショールームを閉館し、課員を全員解雇し、展示物を楽天のコワーキングスペース「ラクネスト」に移した時点で辞め(させてもらい)ました。多少の退職パッケージがもらえるよう、元同僚の社長により、解雇してもらいました。
自分で辞めると失業保険出ませんし、家のローンはスタートアップ転職早々に返済貧乏になりながらも、全額返済してましたから、失職の不安は殆どありませんでした。
そして2023年、66歳でLLCを設立し、独立したというわけです。続きは別ブログで詳しく。
起業に関しては、気持ちの持ちように関して次のようなステージがあります。
実行実践では次の気力がはじめに重要です。「勇気、やる気、本気、元気、活気」ですね。
しばらくすると、失敗してもへこたれない、「負けん気と根気」が要ります。「粘り気」もいいですね。
「前向き」は気じゃないものの、捨てられないキーワードです。
人と組めば大きく出来ると言われます。その時は、「和気、覇気」が必要で、チームを「その気」にさせる「熱気」をいつも心がけなくてはいけません。
組織を大きくするには日立のコマーシャルのダジャレではないですが「木になる気」というマインドが要るようになってきます。
スタートアップへ転身してから15年。HP・アジレント時代に習得したことがなければ、この 15年間は無理だったでしょう。忙しくてもスキルアップは心がけないと自分の進歩を止めてしまいます。これからも新しいことにチャレンジして邁進します。